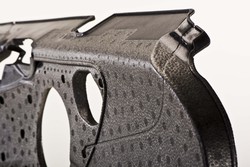
La corsa sfrenata a ridurre sempre più il peso delle auto e abbattere i consumi di carburante, sfocia in una sfida continua e stimolante nella progettazione e fabbricazione dell'industria automobilistica.
In collaborazione con Bert Suffis, Sales & Application Development Manager - Europa, Africa e Medio Oriente, JSP
Sostituendo i tradizionali componenti in acciaio con dei materiali leggeri è possibile ridurre direttamente il peso del corpo e del telaio del veicolo fino al 50% comportando un effetto proporzionale sul consumo di carburante. Una riduzione del 10% del peso del veicolo può comportare un risparmio di carburante dal 6 all'8%.
Lo sviluppo di ARPRO rappresenta una delle principali innovazioni degli ultimi decenni. Sviluppato per la prima volta negli anni Ottanta, questo materiale ha fatto il suo ingresso nell’industria automobilistica europea più di trent’anni fa. Ideale per il design automobilistico, questo materiale possiede capacità di assorbimento dell'energia tali da garantire ai progettisti una stampabilità potenziata. È utilizzato da produttori come BMW e Peugeot per aumentare l'efficienza dei veicoli e raggiungere i primi posti nell'industria automobilistica.
A differenza dei materiali precedenti, le cui capacità di assorbimento dell’energia erano piuttosto discutibili, l’EPP poteva vantare due caratteristiche fisiche fondamentali che gli hanno consentito di imporsi come materiale “di riferimento” per la protezione dagli impatti a bassa velocità. Innanzitutto, la struttura a celle chiuse della sua schiuma lo rende isotropico e gli consente di offrire le stesse prestazioni efficienti indipendentemente dalla direzione dalla quale si riceve l’impatto. Questa caratteristica ha rappresentato una forte differenza rispetto ai prodotti in poliuretano rigidi e stampati a iniezione, le cui prestazioni non possono essere previste con precisione per impatti superiori al 5% oltre la direzione e la velocità previste. L’altro vantaggio dell’EPP è che, pur deformandolo più volte, torna sempre alla sua forma originale, cosa che lo rende ideale per le applicazioni destinate agli impatti a bassa velocità. Queste qualità indicano che questo materiale non solo soddisfa, ma in molti casi supera gli esigenti requisiti di prestazione governativi e industriali, come ad esempio l'EURO NCAP.
Un esempio di punta delle sue tante applicazioni è quello della Peugeot 308. Accolta dagli operatori del settore come un punto di riferimento per il design e l'ingegneria ed elogiata per la sua efficienza e la sua struttura più leggera, è stata nominata “Auto dell'anno” europea per il 2014. Queste caratteristiche sono state ottenute attraverso l'uso intensivo di materiali compositi, la riprogettazione delle aree di impatto e lo sviluppo di applicazioni, compreso un piano di seduta universale, e altri elementi fondamentali che impiegano ARPRO®.
Utilizzato per un totale di sei applicazioni all'interno della 308, ARPRO è considerato uno degli elementi principali grazie al quale è stata possibile una notevole riduzione del peso complessivo dell'auto. L'impiego di questo materiale leggero ha migliorato la sicurezza e le prestazioni, riducendo il consumo di carburante e le emissioni di CO2, mentre il sedile con rampa antisubmarining integrata, interamente costituito in ARPRO, consente la creazione di una struttura piatta e modulare. Facile da montare agganciandolo in posizione, il piano di seduta della 308 elimina la necessità di creare su misura per ogni singolo modello un piano di seduta integrato nel telaio. Questo design ha permesso agli ingegneri di Peugeot di applicare l'innovativo piano di seduta a vari modelli, risparmiando sul peso, sui tempi e sui costi per ogni modello. L'utilizzo a tutto tondo di ARPRO ha contribuito a rendere la nuova 308 più leggera di 140 kg rispetto al modello precedente.
Un altro vantaggio per l'industria automobilistica è costituito dai costi di attrezzaggio che sono significativamente inferiori rispetto a quelli necessari per lo stampaggio a iniezione; inoltre i prodotti leggeri consentono di rimuovere, senza movimentazioni dello stampo, elementi in sottosquadra evitando così senza bisogno di effettuare ulteriori investimenti nelle attrezzature. Con un materiale come ARPRO, si può ridurre del 50% la spesa per gli stampi ottenendo allo stesso tempo una significativa riduzione del peso dei componenti stampati. Esso, inoltre, vanta la capacità di creare parti di maggiore complessità in grado di rispondere a requisiti multi-funzionali per un singolo componente.
Nell'ambito dell'interior design per il settore automobilistico, la BMW i8, recentemente lanciata sul mercato, ha ottenuto un primato grazie all'utilizzo di ARPRO per i pannelli delle portiere. L'apertura ad ali di gabbiano delle portiere di questo modello esclusivo rappresenta un elemento di spicco e sottolineano le caratteristiche sportive dell'automobile. Tuttavia, per consentire questo tipo di design, i pannelli dovevano incorporare un materiale più leggero anche solo per essere sollevati.
ARPRO garantisce prestazioni solide da un punto di vista strutturale e un ottimo assorbimento dei rumori, riuscendo persino ad alterare la frequenza del rumore di un'automobile potente e donando al conducente la migliore esperienza di guida possibile.
È stata fatta molta ricerca in merito alla resistenza alle vibrazioni, soprattutto per quanto riguarda la relazione con un veicolo che invecchia nel tempo ma, grazie a test intensivi svolti congiuntamente ai principali produttori automobilistici, si è scoperto che i livelli di vibrazione non sono maggiori di quelli riscontrati con i telai tradizionali e rientrano senza dubbio nei parametri di sicurezza e comfort accettati. La natura isotropica di ARPRO, ad esempio, indica che l’energia dell’impatto viene rapidamente dissipata in tutte le direzioni.
Lo sviluppo dei veicoli elettrici è anche una risposta alla forte pressione cui è sottoposto il settore automobilistico in materia di emissioni, caratterizzata dalla necessità di adempiere in tempi brevi a obiettivi inderogabili, decisivi e complessi. Entro il 2020 e il 2025 le OEM europee devono ridurre le emissioni medie di CO allo scarico al di sotto di 95 g di CO2/km e poi di 75 g di CO2/km. Pertanto, i produttori sono chiamati ad affrontare una sfida decisiva e un eventuale fallimento nel raggiungimento di questi obiettivi potrebbe risultare catastrofico comportando severe sanzioni su ogni singola vettura non conforme prodotta.
Grazie a materiali efficienti e adattabili come ARPRO, si contribuisce al raggiungimento di nuovi primati nella progettazione e produzione automobilistica. La versatilità dei prodotti leggeri moderni e le nuove tecnologie aiutano i designer a compiere un enorme passo avanti in materia di efficienza. Idealmente collegati alla promozione dello sviluppo di altri concept per la riduzione del peso nel settore automobilistico, i materiali leggeri possono essere impiegati anche in applicazioni automotive diverse, attualmente e in futuro.